In the world of electrical enclosures, the smallest details can have a significant impact on performance and durability. Electrical cabinet hinges, often overlooked, are no exception. The right surface finish can enhance hinge longevity, corrosion resistance, and even improve the overall aesthetic of the cabinet. For engineers, understanding the variety of surface finishing methods available is crucial for ensuring the best outcome in any application. In this article, we will explore the most common surface finishing methods used for electrical cabinet hinges, comparing their advantages and specific uses.
Common Surface Finishing Methods for Electrical Cabinet Hinges
In the field of surface finishing, a few key methods stand out for their effectiveness in protecting electrical cabinet hinges from environmental stressors like corrosion, moisture, and mechanical wear. These methods include electroplating, powder coating, sandblasting, and others. Here is a summary of the most commonly used techniques.
1. Electroplating
- Function: Electroplating is a process where a thin layer of metal, such as zinc, nickel, or chromium, is deposited on the surface of the hinge using an electric current. The main purpose of this coating is to improve the hinge’s corrosion resistance and overall appearance.
- Advantages:
- Corrosion Resistance: Electroplating offers excellent protection against corrosion, making it ideal for outdoor or harsh environments where moisture or chemicals may be present.
- Enhanced Aesthetic: The smooth, shiny finish provided by electroplating is often preferred for its polished, high-quality appearance.
- Improved Conductivity: Electroplating with metals like zinc or nickel can also improve the hinge’s conductivity, which may be necessary in some electrical cabinet designs.
- Common Materials: Zinc, nickel, and chromium are the most frequently used metals in electroplating due to their superior corrosion resistance and aesthetic appeal.
2. Powder Coating
- Function: Powder coating involves applying a dry powder (often epoxy or polyester) to the surface of the hinge. The powder is then heated, causing it to melt and form a hard, protective layer over the hinge.
- Advantages:
- Durable Finish: Powder coating forms a thick, durable layer that is resistant to chipping, scratching, and corrosion, making it ideal for outdoor electrical enclosures.
- Color Variety: Powder coating can be done in a wide range of colors, allowing for customization based on specific design requirements.
- Uniform Coating: The powder coating process results in a smooth, uniform finish that is aesthetically pleasing and consistent.
- Best Applications: Powder coating is especially well-suited for outdoor environments where electrical cabinets may be exposed to harsh weather conditions, moisture, or industrial contaminants.
3. Sandblasting
- Function: Sandblasting, also known as abrasive blasting, is a surface preparation method where abrasive materials are forcibly propelled at the surface of the hinge to clean, smooth, or prepare it for further treatments like powder coating or electroplating.
- Advantages:
- Surface Cleaning: Sandblasting is an effective method for removing rust, paint, and other contaminants from the hinge surface, leaving it clean and ready for finishing.
- Matte Finish: Sandblasting leaves a matte texture, which is often desired for certain aesthetic applications.
- Preparation for Other Methods: While sandblasting does not provide corrosion resistance on its own, it prepares the surface for additional treatments that offer protective qualities.
- Best Applications: Large or heavily used hinges that require a rugged, textured finish benefit from sandblasting, especially as a pre-treatment for more protective coatings.
4. Anodizing
- Function: Anodizing is an electrochemical process commonly used on aluminum hinges to increase corrosion resistance, surface hardness, and wear resistance. It enhances the metal’s natural oxide layer, making it thicker and more durable.
- Advantages:
- Superior Corrosion Resistance: Anodizing significantly enhances aluminum’s ability to withstand corrosion, making it ideal for use in outdoor or harsh environments.
- Surface Hardness: Anodized aluminum has increased hardness, making it more resistant to scratches and wear.
- Decorative Options: Anodizing can be used to produce a variety of colors and finishes, adding aesthetic value to the hinge.
- Best Applications: Aluminum electrical cabinet hinges used in outdoor settings or where a decorative finish is desired.
5. Galvanization
- Function: Galvanization is a process where a layer of zinc is applied to the surface of steel hinges. This zinc layer protects the underlying steel from corrosion, primarily through a process known as “cathodic protection.”
- Advantages:
- Long-Term Rust Protection: Galvanized hinges can resist rust for many years, making this a preferred method for outdoor or industrial applications.
- Low Cost: Galvanization is a cost-effective surface treatment, especially for large-scale production.
- Simple Application: The process is relatively straightforward and can be applied to many types of steel products.
- Best Applications: Hinges for outdoor or industrial electrical cabinets where long-lasting rust protection is critical.
6. Chromating
- Function: Chromating, or chromate conversion coating, is a chemical process used to enhance the corrosion resistance of metals, particularly aluminum, zinc, and copper. It also improves the adhesion of subsequent coatings like paint or powder coating.
- Advantages:
- Enhanced Durability: Chromate coatings increase the durability and lifespan of the metal.
- Adhesion Promotion: Chromating is often used as a pre-treatment before painting or powder coating to improve adhesion.
- Best Applications: Hinges that will undergo additional coating treatments benefit from chromating as it provides a strong base layer for further surface finishing processes.
How to Choose the Right Surface Finishing Method?
Choosing the right surface finish for electrical cabinet hinges depends on several key factors:
Application Environment:
- For outdoor or corrosive environments, powder coating and electroplating are excellent choices due to their superior corrosion resistance.
- Indoor applications with lower exposure to harsh elements may benefit from simpler finishes like galvanization or chromating.
Material Type:
- Aluminum hinges are best paired with anodizing, which enhances both corrosion resistance and appearance.
- Steel hinges can be protected with galvanization or electroplating, depending on the specific environmental requirements.
Aesthetic Considerations:
- Powder coating offers a wide variety of colors and finishes, making it ideal for projects with specific aesthetic requirements.
- Electroplating provides a smooth, polished appearance that is often preferred for high-visibility applications.
The Impact of Surface Finish on Hinge Performance
Corrosion Resistance:
Surface finishing methods like powder coating, electroplating, and anodizing significantly enhance the corrosion resistance of electrical cabinet hinges. For example, powder-coated hinges can withstand exposure to moisture and harsh chemicals for longer periods, while electroplated hinges resist rust and corrosion in various environments.
Durability:
The right surface finish can improve the durability of hinges, making them more resistant to wear, abrasion, and environmental factors. Galvanization provides long-term rust protection, while anodizing enhances the hardness and scratch resistance of aluminum hinges.
Electrical Conductivity:
For hinges that require conductivity, electroplating with metals like nickel and zinc ensures that the hinge maintains its conductive properties while still being protected from corrosion.
Cost and Efficiency of Surface Finishing Methods
Each surface finishing method has its own cost considerations, which can affect the choice depending on the scale of production and the specific needs of the project.
Electroplating:
- Cost: Typically more expensive, especially when using high-quality metals like nickel or chromium.
- Efficiency: Provides excellent long-term protection but requires careful application.
Powder Coating:
- Cost: Cost-effective for large-scale production.
- Efficiency: Highly durable and versatile in terms of color and finish options.
Sandblasting:
- Cost: A relatively low-cost option.
- Efficiency: Best used as a pre-treatment before applying more durable finishes like powder coating or electroplating.
Environmental Protection: Our Commitment to Sustainable Practice
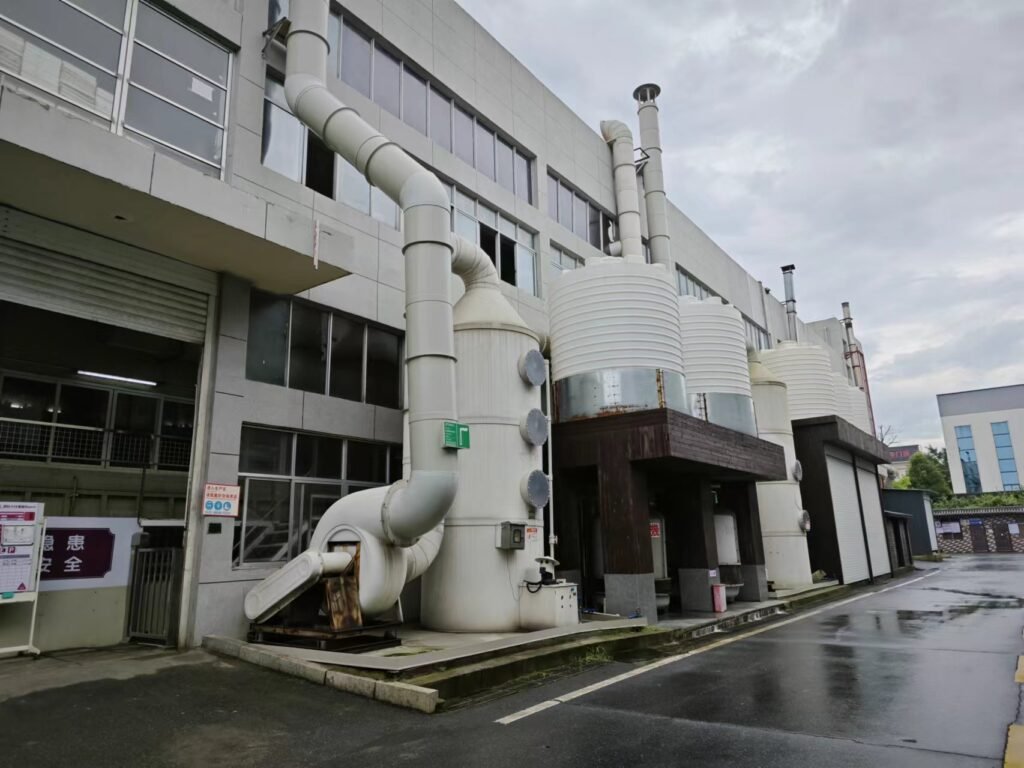
At Hingelocks, we believe in protecting the environment while maintaining the highest standards of quality in surface finishing. Our factory is equipped with its own wastewater treatment plant and advanced environmental protection equipment. This allows us to responsibly treat all waste and pollutants generated during the finishing processes, ensuring compliance with environmental regulations. Through our commitment to sustainability, we ensure that our products not only meet industry standards but also contribute to a healthier planet.
Conclusion
The choice of surface finishing method for electrical cabinet hinges plays a critical role in determining their durability, functionality, and resistance to environmental factors. Electroplating, powder coating, and sandblasting are among the most common and effective methods available. Engineers should evaluate the specific application environment, material type, and desired aesthetics when selecting the appropriate surface finish to ensure optimal performance and longevity.